自動車製造や、医療機器製造業などにかかわる精密加工業の皆さまへ。
外観検査において、業界ならではの課題を解決いたします。
このようなことでお困りではないですか?
外観検査の困りごと解決します
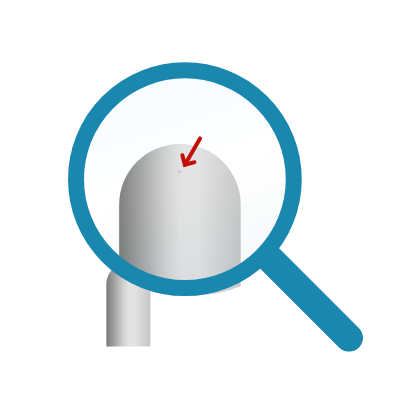
欠損をうまく見つけられない
見つけられない一例
- 曲面・鏡面にある欠損は光が反射してうまく見つけられない
- 加工痕と同化してしまう欠損をうまく見つけられない
- 透明体にある欠損は光が偏向・反射してうまく見つけられない
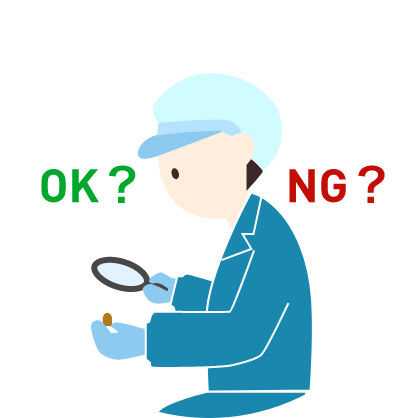
判定が安定しない
安定しない一例
- 人間に依存しているのでヒューマンエラーやばらつきがあり安定しない
- 熟練した作業者が必要だが、その育成時間・コストがかけられない為安定しない
- 自動化を導入したが条件設定が難しく判定が安定しない
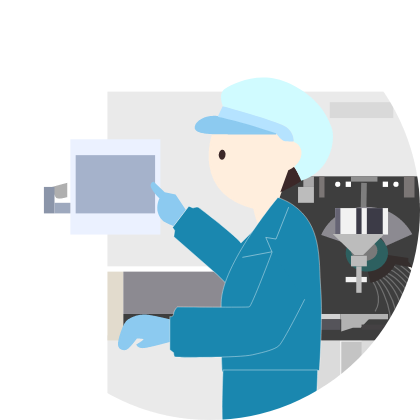
検査結果を製造工程にフィードバックできない
製造工程にフィードバックできない一例
- 欠損をデータ化・分析出来ない
- 検査結果を逸早く製造現場に反映出来ない
- 蓄積した検査データが簡単に確認・活用出来ない
HUMOの自動外観検査装置でできること
見つける

判定する

欠損のデータ化

省人化
欠損を見つける技術
3つの「画像検査技術」で曲面・光沢、加工痕、透明体などの検査しにくい対象物も可能に。微細な欠損も見逃しません。
1. 曲面・鏡面にある欠損
対象物:光沢がありハレーションの強い曲面、球面のある小型部品など(10センチ程度まで)
曲鏡面で構成される部品は光が反射するため欠損を見つけるのは難しく、人間の目でも角度を変えて何度も観察しないと見つけられません。また、映りこんだ影と欠損を区別することも難しいです。当社では特定の光パターンを検査対象物に反射させその変形具合を画像解析することで欠損を検出する方法を開発しました。これにより数十マイクロメートルの浅い欠損でも、角度を変えて何度も観察する手間をかけずに安定した検出ができます。
曲面の欠損検出事例
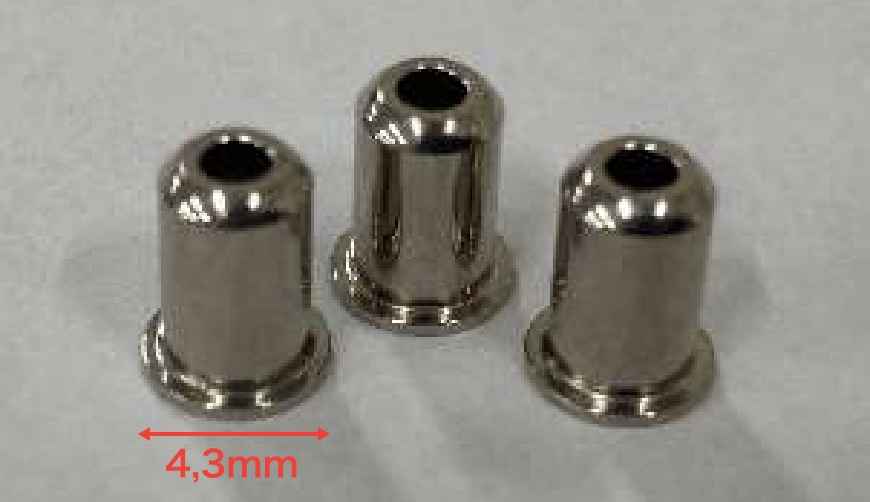
対象物例:曲面体の部品
曲面体の部品の真上から見た対象物
パターンを照射することにより微細な傷を検出
2. 加工痕と同化してしまう欠損
対象物:数十μ単位の精密切削加工した小型部品など。(10cm以下)
例えば切削加工部品など表面に加工痕のあるものに有る数十マイクロメートルの欠損は、加工痕と同化してしまい見つけることは簡単ではありません。当社では、画像を周波数解析する事により加工痕と欠損を区別し数十マイクロメートルの巣穴も正確に検出できます。巣穴に限らず他の傷でも可能です。
加工痕の欠損検出事例
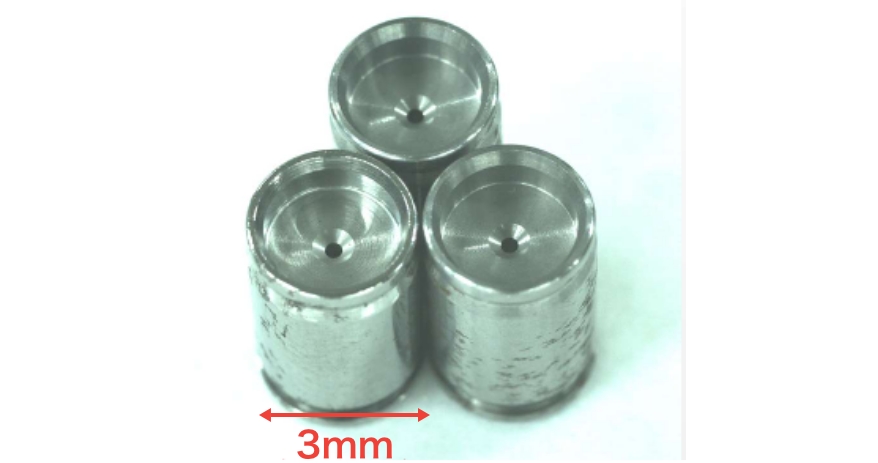
対象物:切削加工部品
切削加工部品を真上からの撮影
加工痕と見極めが難しい巣穴を検出する為に特殊な画像処理を行い欠損を検出
3. 透明体や半透明体にある欠損
対象物:透明体、半透明体のもの
透明体や半透明体は、光が偏向・反射するため欠損を見つけるのは難しく、従来は人間の目で検査を行っていました。当社では複数色の光源の採用と外乱光や検査対象物の個体差による影響を抑えるアルゴリズムにより透明体や半透明体の表面及び内部状態を正確に検出できます。対象物のサイズは問いません。光を通す物質であれば硬度等も問いません。
透明体の欠損検出事例
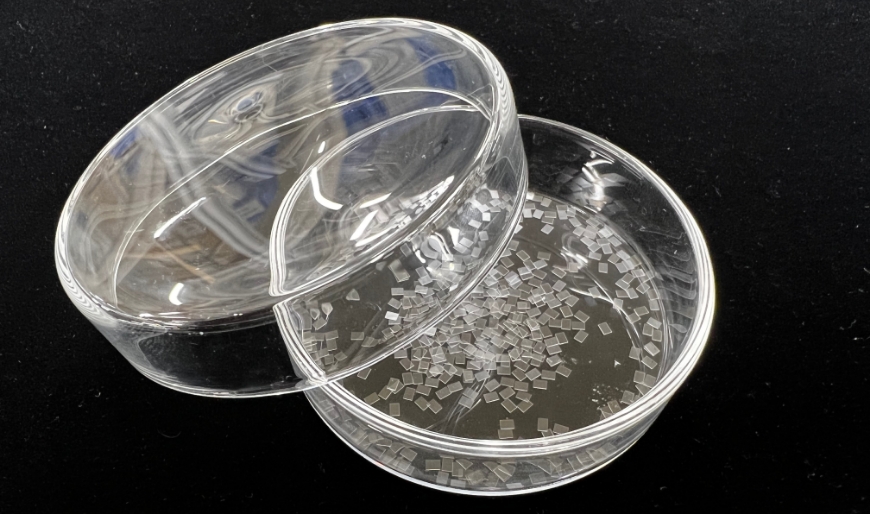
対象物:透明(わずかに乳白色)な水晶板
2色照明で撮像
右画像:赤色情報のみで処理を行い変色を検出
欠損を判定する技術 安定した判定を実現する技術
機械化により安定した判定を得る
人間による目視検査は、ヒューマンエラーや検査員の判定にバラツキが生じ易いという問題があります。それに対して、カメラ画像を画像処理して判定する自動外観検査は常に安定した判定ができます。
柔軟な判定アルゴリズムと判定条件の共用により安定した判定を得る
人の直感的な判断は機械よりも優れていますがその判断基準を正確に他者に伝える事は難しいものです。当社では対象物に応じて欠損の大きさや長さだけでなく、形の特徴、色などの判定基準を最適化するアルゴリズムにより人の判断に近い判定を可能としその判定条件をデータ化し共用します。これにより検査対象の切り替え・検査数の増加があっても安定した判定ができます。
容易な判定条件の設定により安定した判定を得る
自動化しても、判定の条件設定が難しくて過剰判定となり歩留まりが悪化したり、逆にNG判定が甘くなることがあります。当社では機械学習による中間判定に数値条件の判定を組み合わせることで過剰ではない、現実的な判定ができます。
機械学習には通常1万個ほどのサンプル登録が必要とされ、その登録の手間が課題です。
当社では機械学習を中間判定に限定利用する事で100個程度の良品サンプル登録で安定した判定ができます。
検査結果を製造工程にフィードバックする技術
欠損具合を数値化・分類できる
外観検査は、必要不可欠な工程ですが、品質を改善することはできません。改善するには欠損の具合をデータ化して製造工程にフィードバックすることが必要です。外観検査をシステム化する事により欠損の内容を数値化・分類、集計してデータ蓄積し活用して頂けます。
検査結果を素早く反映できる
当社装置では1つ1つの欠損データ、判定結果・分類統計データや画像データの分類・保存は勿論の事、判定結果を統計的に処理しリアルタイムに検査状況を確認頂く機能により素早く製造工程へフィードバック活用して頂けます。
蓄積したデータを簡単に活用できる
ネットワークを利用したリアルタイムなデータの共有・集約機能を用意し、ご要望に合わせて集中管理するシステムをご提供します。これにより複数の装置、膨大な検査数であっても簡単にデータを集約・活用して頂けます。
ヒューモラボラトリーについて
省人化する技術・自動検査装置への取り組み
人間の感覚に頼った検査は、検査員を確保してスキルを教育しなくてはなりません。さらにはヒューマンエラーやばらつきをゼロにすることも不可能です。これらの問題を解決するには、自動外観装置を導入して省人化をすることがベストな方法です。
また現在の製造現場では歩留まり改善や品質管理が非常に重要な課題となっており、検査装置には生産ラインと連携できるシステムが必須となっています。
当社には欠損を見つける技術と欠損を判定する技術に加えて、電子部品の自動検査装置で50年間積み重ねてきた、搬送技術や制御技術・ネットワーク技術があります。これらの技術を組み合わせることで、供給→搬送→検査→分類→データ処理・集約までをシステム化し使いやすいマンーマシンインターフェースを備えた自動外観検査装置の提案をいたします。
ある調査によると外観検査工程の省人化は半自動を含めても40%に満たないようです。省人化に踏み切れない理由は様々ですが、その解決に当社をお役立てください。
主な取引先企業
太陽誘電、京セラ、村⽥製作所、YAGEO、サムスン電機、CCTC、⼤真空、シチズンファインデバイス、⽇本電波⼯業他多数
どのような問題でも
まずはお気軽にご相談ください。
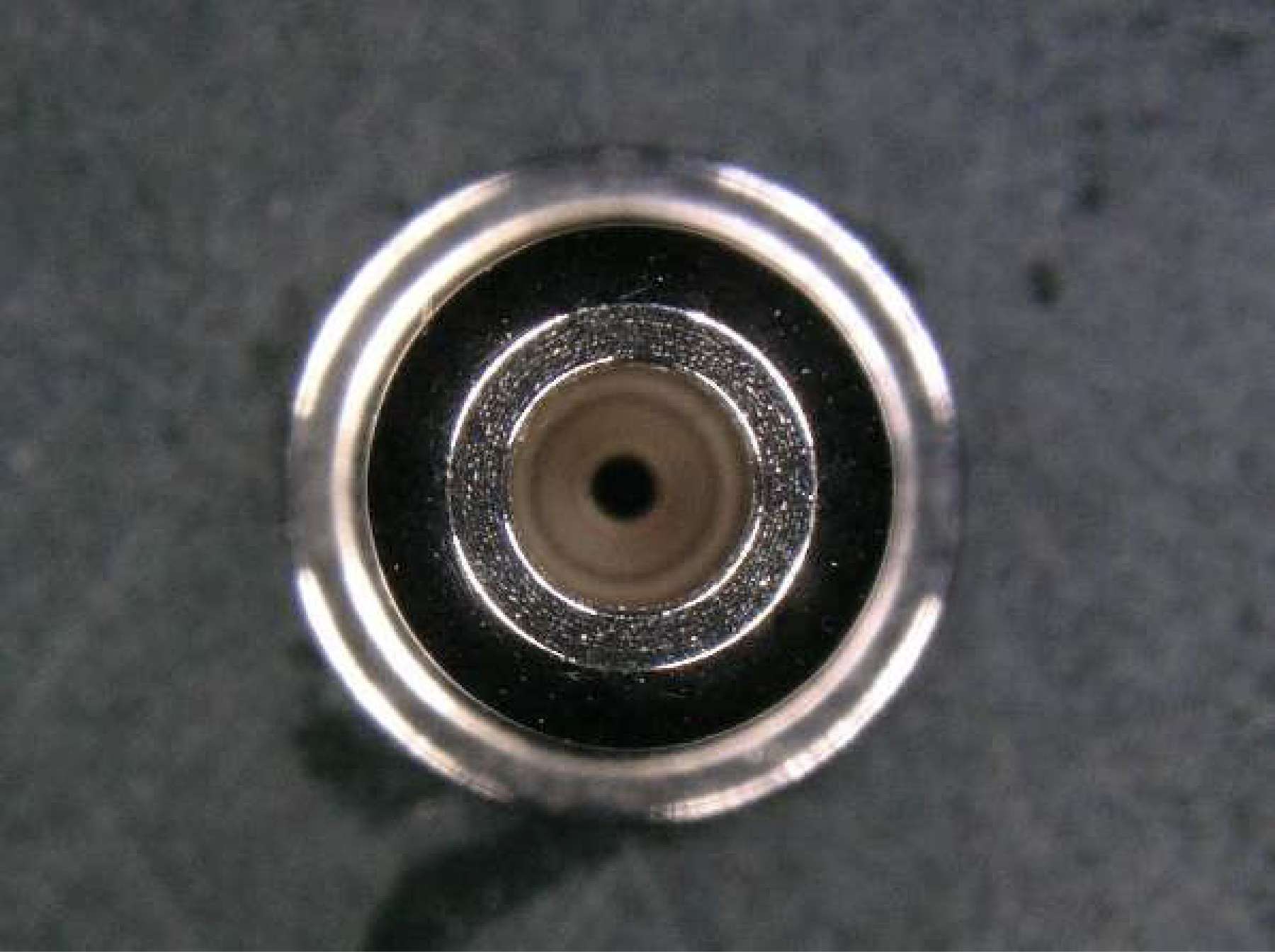
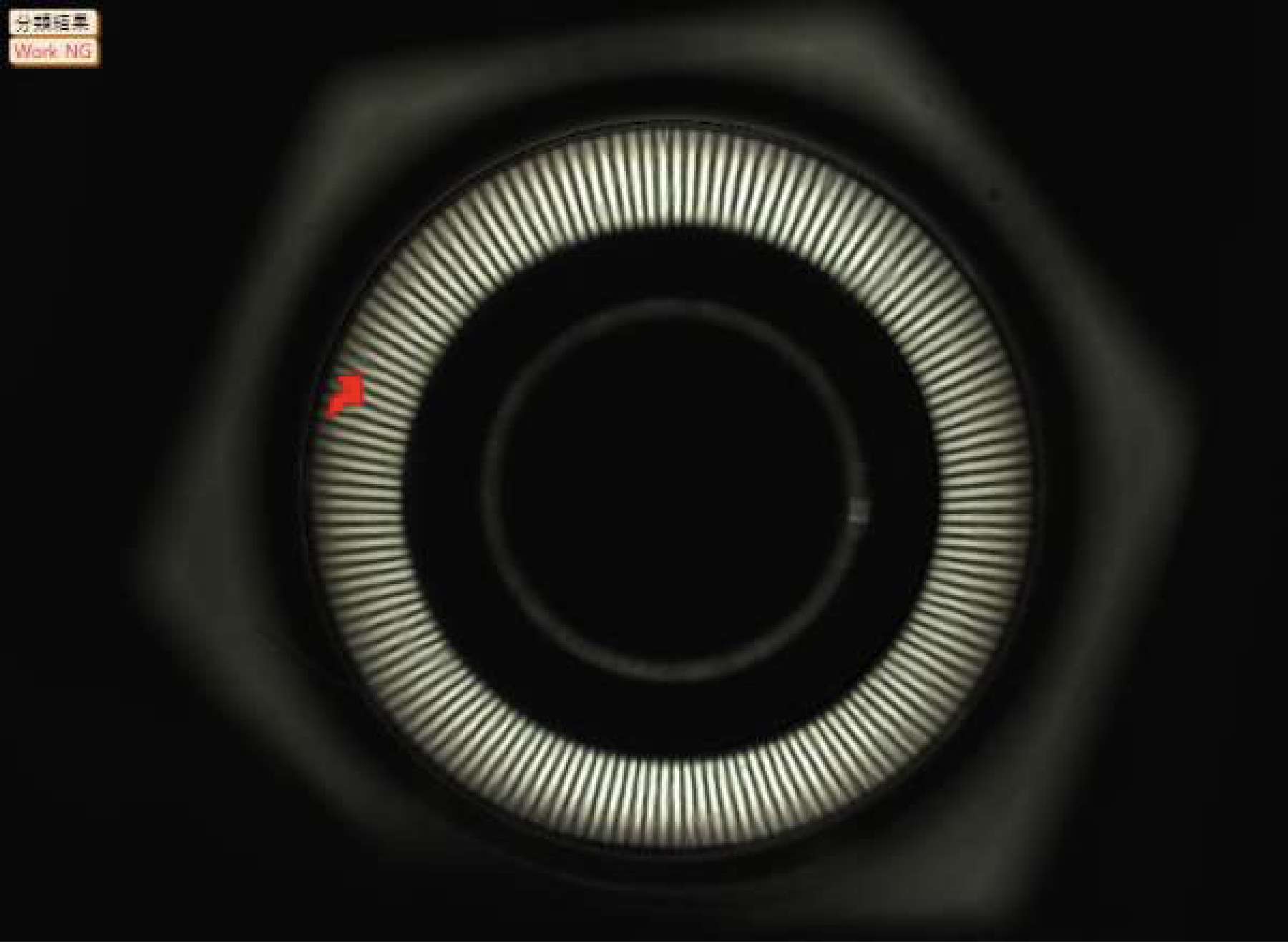
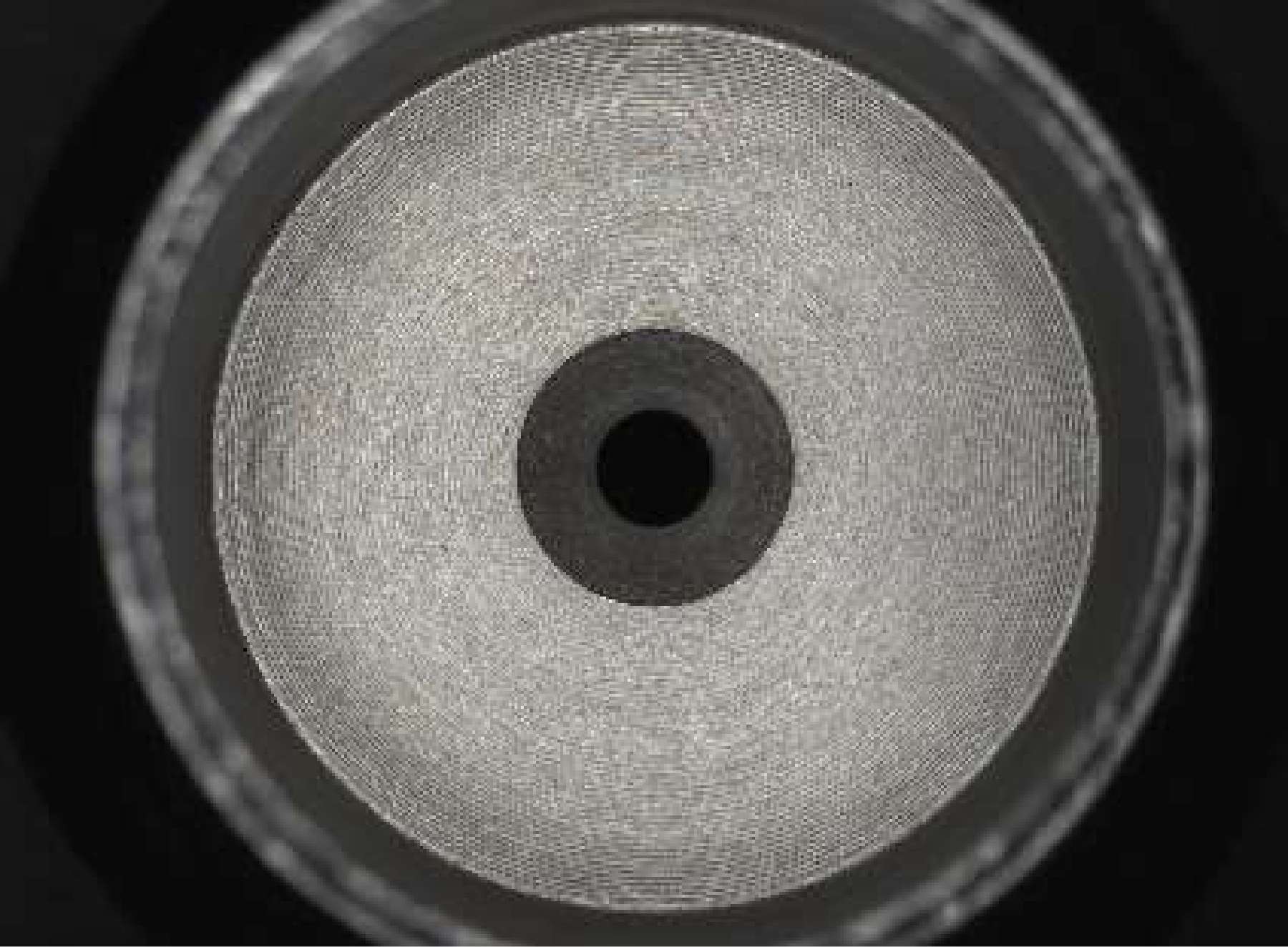
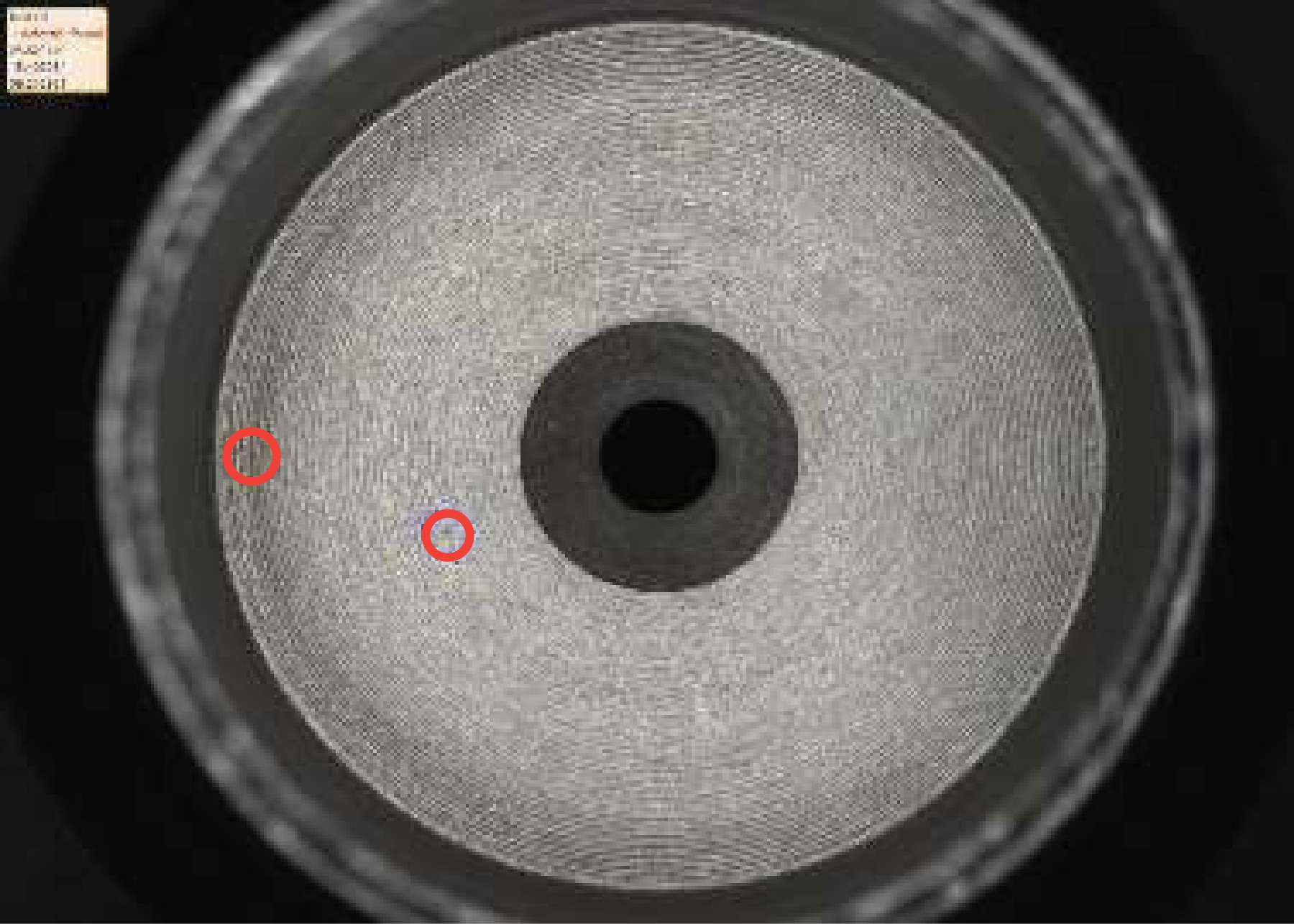
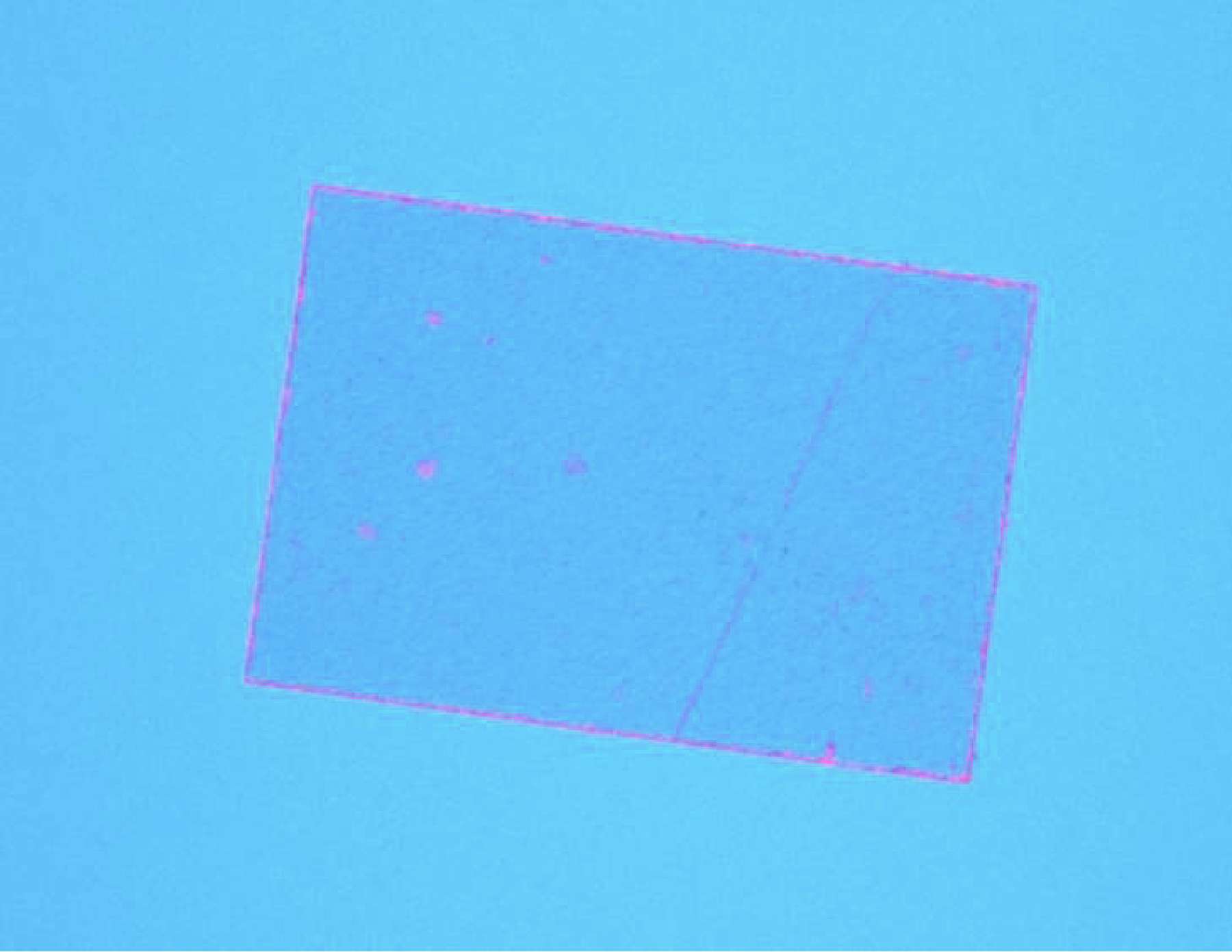
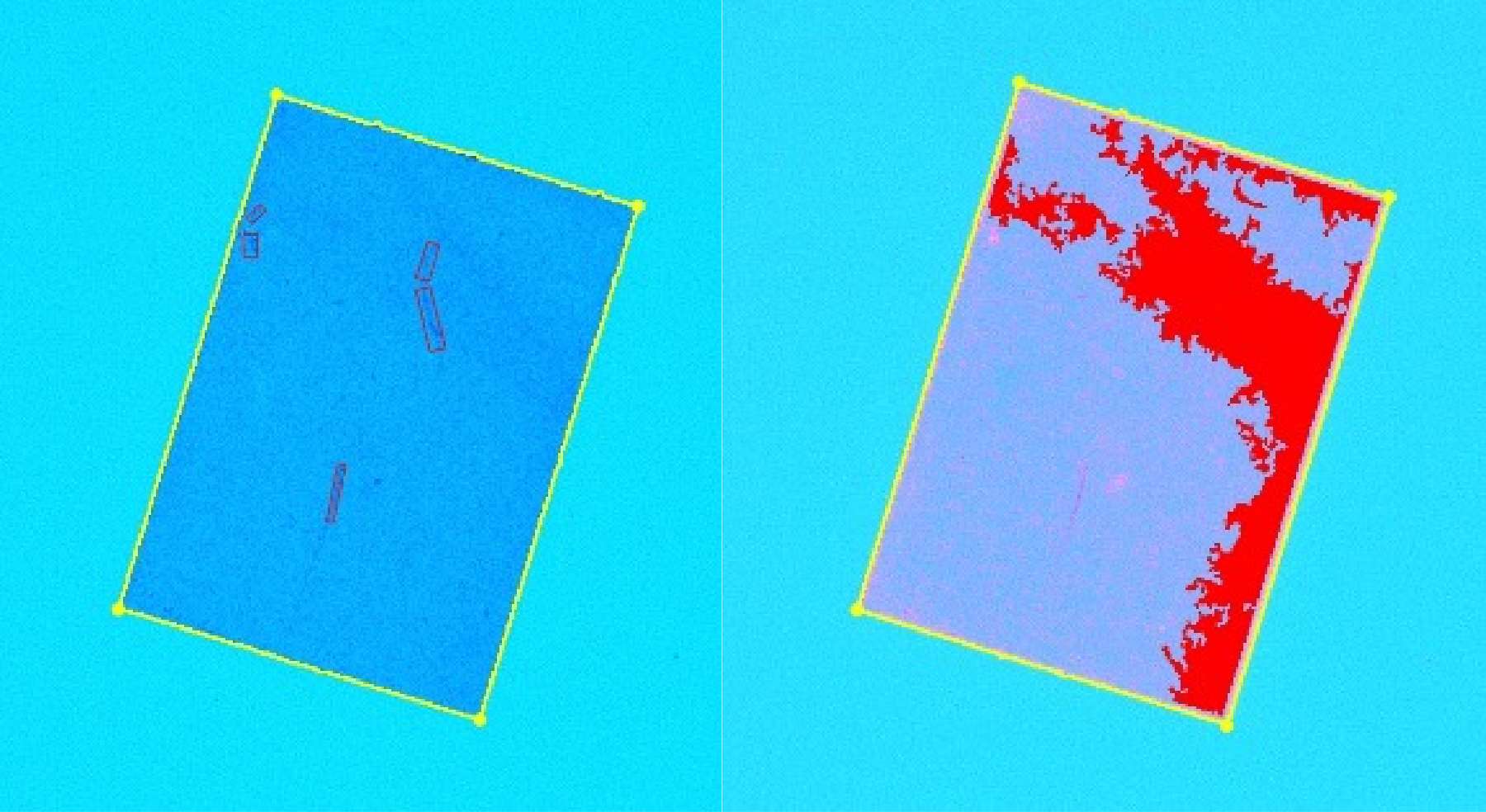